MS25 OPERATION MANUAL
SAFETY INSTRUCTIONS
Please read these instructions carefully. Failure
to follow these instructions could result in severe injury.
1. |
Before using the tool read the
entire operation manual thoroughly. |
2. |
Always wear safety glasses and
face protection when operating the tool. |
3. |
Always wear protective gloves when
handling strapping. |
4. |
Always use only replacement
parts from an authorized dealer. |
|
These tools are designed for use with high tensile strapping
and all parts are manufactured or treated for these extreme
conditions. Performance of your tool will be affected if any
other parts are used, which may cause injury. |
top of page
SPECIFICATIONS
Model Number
|
Strap Width
|
Strap Thickness
|
MS25-1
|
1/2" (13 mm)
|
.020" - .025" (0.5 mm - 0.635
mm)
|
MS25-2
|
5/8" (16 mm)
|
.020" - .025" (0.5 mm - 0.635
mm)
|
MS25-3
|
3/4" (19 mm)
|
.020" - .025" (0.5 mm - 0.635
mm)
*.015" - .019 (038 mm - 0.48 mm) requires knife ZR-0070
|
This tool is
not to be used with material above .025"
thickness
.
Weight: |
9.4 lbs |
(4.25 kg) |
Base Length: |
4.5" |
(115 mm) |
Base Width: |
2.4" |
(60 mm) |
Height: |
4.2" |
(105 mm) |
STRAPPING QUALITIES
Designed for use with regular duty strapping (107,000 PSI / 750
N/mm2) to high tensile strapping (156,000 PSI / 1100
N/mm2).
top of page
OPERATING
INSTRUCTIONS
A
Place strapping tightly around the package and hold in
place with left hand.
Take tool with right hand and pull the feedwheel lever
towards the sealing lever.
Insert both portions of the strap with left hand into the
sealing section. Release the feedwheel lever and make certain
strapping is held by strap guide.
|
|
B
Hold tool firmly with left hand on the sealing lever.
With right hand move the tension lever forward and backward
until the desired tension is obtained.
|
|
C
Place right hand firmly on the tension lever for supporting
the tool.
With left hand push the sealing lever forward until it
reaches the stop.
|
|
D
Move the sealing lever back to its original position.
To release the tool, with right hand pull the feedwheel
lever towards the sealing lever, pushing the lever to the
left away from the sealing section.
|
|
top of page
MAINTENANCE
Clean the sealing section regularly with compressed air to remove
any dust and particles.
Lubricate daily with a thin grade of oil the die (position 16)
and punch (position 26).
This will reduce friction and extend tool as well as part life.
top of page
ADJUSTMENTS
TO ADJUST SEALING DEPTH
Loosen nut (position 33), adjust hexagon socket set screw (position
46) with a hexagon key, turn counterclockwise to increase sealing
depth, or turn clockwise to decrease sealing depth, re-tigthen
nut.
TO ADJUST CLEARANCE BETWEEN THE FEEDWHEEL (POSITION 5) AND
GRIPPER (POSTION 27)
The clearance between the feedwheel and the gripper should
be .012" (.31 mm). If the clearance is more or less than
this, it must be adjusted.
To reduce the clearance: loosen nut (position 33A), turn
hexagon socket set screw (position 32) counterclockwise with a
ball hexagon key, re-tighten nut.
To increase the clearance: loosen nut (position 33A), turn
hexagon socket set screw (position 32) clockwise with a ball hexagon
key, re-tighten nut.
top of page
REPLACEMENT OF PARTS
*Please Note: If you are not familiar with the following replacement
procedures, please contact your authorized

dealer
for a demonstration or for service.
To Replace The Feedwheel (Position 5)
1. |
Remove external retaining ring
(position 3). |
2. |
Remove tensioning assembly (consisting
of tension lever (position 11) and feedwheel shaft (position
2)). |
3. |
Install new feedwheel with the
"O" marking facing the strap guide (position 4),
re-install tensioning assembly observing the key way position
during assembly. |
4. |
Re-position strap guide onto the
protruding feedwheel shaft. |
5. |
Re-install external
retaining ring. |
To Replace The Gripper (Position 27)
Note: The gripper is held in a non-adjustable
position with spring tension pin (position 28).
1. |
To remove
gripper, use drift pin matching the dimension of the spring
tension pin (position 28) and drive the tension pin into the
tool base, until the gripper comes loose from it's position. |
2. |
Lift feedwheel lever (position
7) to access gripper. |
3. |
Clean cavity area and add one drop
of a thin grade of oil in the cavity. |
4. |
To install new gripper, place the
gripper into the cavity of the tool base. Re-install the spring
tension pin and drive it into the hole of the tool base, until
it is flush with the tool base. |
To Replace The Knife (Position 17)
1. |
Remove housing cover (position
52), by removing 4 hexagon socket shoulder screws (position
50). |
2. |
With pliers pull knife from slot
on die and knife block (position 13). |
3. |
Install new knife observing spring
tension pin (position 18) aligns with same slot on die and
knife block. |
4. |
Make sure area is clean and well
greased. |
5. |
Re-install housing cover, then
re-install hexagon socket shoulder screws with a drop of Loctite*
No. 222 on the thread of each screw. |
To Replace The Punch (Position 26)
1. |
Remove 2 cheese head machine screws
(position 24) located on the underside of the tool base. |
2. |
Remove punch, clean area, replace
with new punch, then re-install cheese head machine screws
with a drop of Loctite* No. 222 on each screw. |
To Replace The Die (Position 16)
1. |
Remove housing cover (position
52), by removing 4 hexagon socket shoulder screws (position
50). |
2. |
Remove sealing lever (position
49), by loosening hexagon socket cap screw (position 48). |
3. |
Remove woodruff key (position 1). |
4. |
Remove eccentric shaft (position
55). |
5. |
Remove the total internal assembly
by titling it at a 20 degree angle (see diagram below) and
pull out with pliers by eccentric shaft plunger (position
57), at the same time making sure to hold internal assembly
together with other hand, exposing die on the underside of
the die and knife block (position 13). |
6. |
Remove 2 cheese head machine screws
(position 15). |
7. |
Remove die, clean area, and replace
with new die, then re-install cheese head machine screws with
a drop of Loctite* No. 222 on each screw. |
8. |
To re-install the internal assembly
follow above procedures in reverse order. |
9. |
Re-install the eccentric shaft
observing it's relative position to the cam (position 36). |
10. |
The cam lever (position 54) must
engage with it's tip into the cavity of the cam. The components
should align together and operate smoothly, please do not
force the parts together. |
11. |
Make sure area is clean and well
greased. |
12. |
Re-install housing cover, then
re-install hexagon socket shoulder screws with a drop of Loctite*
No. 222 on the thread of each screw. |
13. |
Re-install woodruff key and sealing
lever. |
*Loctite is a registered trademark of the Loctite
Corporation.
Removal of Internal Assembly MS25 |
 |
top of page
Installation of Internal Assembly MS25
Figure 1A
Place the cam as per drawing, with the long width sitting
flat in the die and knife block. Add white grease throughout.
Then place the eccentric shaft plunger on top of the cam
and fasten by pushing the connection pin, position 19,(making
sure the groove on this pin is facing the outside of the
die and knife block) through hole in die and knife block
and into like hole on eccentric shaft plunger.
|
|
Figure 1B
Tilt the internal assembly approximately 20 degrees and
place into housing making sure the back up hook is sitting
in its slot in the housing.
|
|
Figure 1C
Make sure the cam lever is attached to the eccentric
shaft. Then push it through the hole of eccentric shaft
plunger and the housing until it is flush.
|
|
Figure 1D
Turn the cam with pliers in a clockwise direction until
it sits in position shown in this drawing.
|
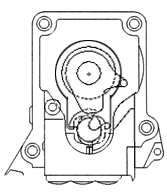
|
Figure 1E
Turn cam lever in a clockwise direction with fingers
until it sits in front of the cavity of the cam.
Important: Make certain that the roller (position 59)
is in its position.
Then install the housing cover and the sealing lever
making sure they sit properly and operate smoothly, do
not force.
|
|
top of page
MS25
DIAGRAM
|
This Diagram is available in a Portable Document Format
(PDF) file. To view it, you need to have Adobe Acrobat Reader
version 4.0 installed on your system. Acrobat Reader is
available as a free download from the Adobe Acrobat Reader
site.
These documents are fully printable and searchable. For
complete information on using Adobe Acrobat features, including
the option of downloading a free copy of Acrobat Reader
4.0, go to the Adobe
Acrobat Reader site. |
Top of page
Position
|
Part Number
|
Part Name
|
Parts per Tool
|
1,1A |
ZR-0001 |
Woodruff Key |
2
|
2 |
ZR-0002 |
Feedwheel Shaft |
1
|
3 |
ZR-0003 |
External Retaining Ring |
1
|
4 |
ZR-0004 |
Strap Guide 1/2" (13mm) |
1
|
4 |
ZR-0005 |
Strap Guide 5/8" (16 mm) |
1
|
4 |
ZR-0006 |
Strap Guide 3/4" (19 mm) |
1
|
5 |
ZR-0007 |
Feedwheel 25 |
1
|
6 |
ZR-0008 |
Roller Bearing |
1
|
7 |
ZR-0009 |
Feedwheel Lever |
1
|
8 |
ZR-0010 |
Washer |
1
|
9 |
ZR-0011 |
Roller Clutch and Bearing Assembly |
1
|
10 |
ZR-0012 |
Roller Clutch |
1
|
11 |
ZR-0013 |
Tension Lever |
1
|
12 |
ZR-0014 |
Handle |
2
|
13 |
ZR-0015 |
Die and Knife Block |
1
|
14 |
ZR-0016 |
Dowel Pin |
2
|
15 |
ZR-0017 |
Cheese Head Machine Screw |
2
|
16 |
ZR-0018 |
Die 1/2" (13 mm) |
1
|
16 |
ZR-0019 |
Die 5/8", 3/4" (16mm, 19mm) |
1
|
17 |
ZR-0020 |
Knife (includes ZR-0021) |
1
|
17 |
ZR-0070 |
Knife 15 for strap thickness of .015"
- .019"
(0.38 - 0.48mm) only. (includes ZR-0021) |
1
|
18 |
ZR-0021 |
Spring Tension Pin |
1
|
19 |
ZR-0022 |
Connection Pin |
1
|
20 |
ZR-0023 |
Back Up Hook |
1
|
21 |
ZR-0024 |
Spring Tension Pin |
2
|
22 |
ZR-0025 |
External Retaining Ring |
2
|
23 |
ZR-0026 |
Shaft |
1
|
24 |
ZR-0027 |
Cheese Head Machine Screw |
2
|
25 |
ZR-0028 |
Dowel Pin |
2
|
26 |
ZR-0029 |
Punch 1/2" (13mm) |
1
|
26 |
ZR-0030 |
Punch 5/8", 3/4" (16mm, 19mm) |
1
|
27 |
ZR-0031 |
Gripper |
1
|
28 |
ZR-0032 |
Spring Tension Pin |
1
|
29 |
ZR-0033 |
Cheese Head Machine Screw |
2
|
30 |
ZR-0034 |
Spring Tension Pin |
2
|
31 |
ZR-0035 |
Strap Stop Front 1/2" (13mm) |
1
|
31 |
ZR-0036 |
Strap Stop Front 5/8" (16mm) |
1
|
31 |
ZR-0037 |
Strap Stop Front 3/4", 1 1/4" (19mm,
32mm) |
1
|
32 |
ZR-0038 |
Hexagon Socket Set Screw |
1
|
33,33A |
ZR-0039 |
Nut |
2
|
34 |
ZR-0040 |
Extension Spring |
1
|
35 |
ZR-0041 |
Hexagon Socket Cap Screw |
1
|
36 |
ZR-0042 |
Cam |
1
|
37 |
ZR-0043 |
Ball |
1
|
38 |
ZR-0044 |
Compression Spring |
1
|
39 |
ZR-0045 |
Die Block Back Up |
1
|
40 |
ZR-0046 |
Spring Tension Pin |
1
|
41 |
ZR-0047 |
Spacer |
1
|
42 |
ZR-0048 |
Pin |
1
|
43 |
ZR-0049 |
Strap Stop Rear 1/2" (13mm) |
1
|
43 |
ZR-0050 |
Strap Stop Rear 5/8" (16mm) |
1
|
43 |
ZR-0051 |
Strap Stop Rear 3/4" (19mm) |
1
|
44 |
ZR-0052 |
Nut |
1
|
45 |
ZR-0053 |
Housing MS25 |
1
|
46 |
ZR-0054 |
Hexagon Socket Set Screw |
1
|
47 |
ZR-0055 |
Roller Bearing |
1
|
48 |
ZR-0056 |
Hexagon Socket Cap Screw |
1
|
49 |
ZR-0057 |
Sealing Lever |
1
|
50 |
ZR-0058 |
Hexagon Socket Shoulder Screw |
4
|
51 |
ZR-0059 |
Roller Bearing |
1
|
52 |
ZR-0060 |
Housing Cover |
1
|
53 |
ZR-0061 |
Cheese Head Machine Screw |
2
|
54 |
ZR-0078 |
Cam Lever |
1
|
55 |
ZR-0063 |
Eccentric Shaft |
1
|
56 |
ZR-0064 |
Roller Bearing |
1
|
57 |
ZR-0065 |
Eccentric Shaft Plunger
(includes ZR-0043, ZR-0044, ZR-0064, ZR-0075) |
1
|
58 |
ZR-0075 |
Spring Tension Pin |
1
|
59 |
ZR-0076 |
Roller |
1
|
60 |
ZR-0077 |
Roller Pin |
1
|
-- |
ZR-0066 |
Operation Manual and Parts List for MS25 Series
Tools |
1
|
Top of page
Click here for Trade Sheet Back
Email Us